(Textile Knowledge) The effect of dyed fabric rubbing fastness
2015-07-02
Rubbing fastness is a textile color fastness test, but also in the course of trade in textiles, one of the most common test items, it refers to the degree of fade through friction dyed fabric after the dye is the assessment of resistance to mechanical friction capacity, divided into dry and wet friction rub, the principle is to use the provisions of the textile sample size of the sample clamp secured to friction tester platform, and then separately with a dry cloth and a wet friction rubbing cloth friction, Finally, the degree of staining white as an evaluation basis, against a standard Grey card, is divided into five levels, the greater the level indicates better rubbing fastness, rubbing fastness of fabric difference will seriously affect its use. Affect the fabric rubbing fastness of a number of factors, following one of several factors.
1.1 Effect of the fabric surface morphology
Because unfixed dye is caused by rubbing fastness main reason for poor, under dry conditions, the surface roughness or buffing, fluff fabric, hard as hemp fabric, denim fabric and pigment printing fabric, if dry friction easily deposited on the surface of the fabric dyes, paints or other colored substance grind down, even causing some colored fiber breakage and the formation of colored particles, so resistance to dry friction color fastness to decline further. For buffing or pile fabric, the pile surface of the fabric surface with rubbing cloth was a certain angle, not parallel, so that the friction head reciprocates when the friction increases, so that this type of fabric resistance to dry rubbing fastness decline.
1.2 Effect of fabric structure
On the impact of surface morphology of fabric structure and fabric rubbing fastness, people did not give much attention. Sample surface thin fabric (usually synthetic or silk fabric), as fabric structure is relatively loose, during dry friction, kinetic friction with the sample will head occurs under pressure and friction sliding portions, so that the frictional resistance is increased, and efficiency of friction. But during the wet friction, the situation is completely different with the cellulose fibers. As the fiber is extremely low moisture absorption or water puffing effect is not obvious, and the presence of water plays a role in the lubricant, which makes such fabrics moisture friction color fastness was superior resistance to dry friction color fastness, which people usually think of textile products should be better than dry friction color fastness rubbing fastness of the concept of moisture in sharp contrast, and often cause people to doubt.
Thus, certain fabrics, superior moisture resistance to dry friction color fastness rubbing fastness phenomenon is not uncommon. In this case, the choice of dye variety, performance dyes, dyeing and finishing process conditions, although there will be an impact on rubbing fastness, compared with the organizational structure and the surface morphology and other physical factors of the fabric, it It seems not very important. Statistics show that this occurs mostly dark or products, such as black, red and dark blue and so on. Of course, corduroy, denim and other fabrics for pigment printing, in wet conditions, due to the dye and dyeing process and other reasons of its own use, the moisture friction color fastness is usually two, or even lower, and not superior to its resistance to dry friction color fastness.
1.3 Effect of reactive dyes chemical structure
When dyeing with reactive dyes cellulosic fiber textile during moisture friction color fastness test, factors that cause color shift are mainly two: First, the friction in the water-soluble dye is transferred to the friction fabric, so as to fade and rubbing cloth staining; the second is part of the broken fibers dyed in friction, formation of tiny colored fiber particles and transferred to the friction fabric, causing staining. Therefore, reactive dyes may affect the color fastness to wet rub resistance factors are: Dyes own structure and properties; the nature of the fabric; the effect of pre-treatment, the fabric damage and surface finish, etc.; soaping after dyeing effect and dyeing; fabric After finishing impact dyed fabrics; fixing treatment effect after dyeing.
Studies have shown that, although the strength of covalent bond with the cellulose fiber reactive dyes of different chemical structure is formed, there are some key differences between stability and adhesion, but the impact on dyed fabrics moisture friction color fastness but no significant differences . Dyeing fabric wet friction, covalent bond formation between dye and fiber will not break and produce floating color. Dye transfer occurs usually supersaturated, not formed a covalent bond with the fibers, van der Waals forces alone generate dye adsorption, so-called floating color.
1.4 Dyeing extent
The study also demonstrated that depth moisture friction color fastness and dyeing of fabrics dyed with reactive dyes closely related that during the wet friction, the amount of color shift and dyeing depth near a good linear relationship, which, when dyed dye Saturation is the most important factor, when dyeing dark, the higher the concentration of the dye used, but not much higher than the saturation value, since the excess dye and fiber can not be combined, but only to form a floating color deposited on the surface of the fabric, seriously affecting fabric moisture friction color fastness. Moreover, non-cotton fiber special treatment occurs under wet conditions swollen, friction increases, fiber strength decline, these are colored fiber breakage, loss and transfer of colors to create good conditions. Therefore, before dyeing cellulose fibers proper pre-treatment, such as silk, singeing, cellulose finish treatment, scouring, bleaching, washing, drying, improve the surface finish of the fabric and the capillary effect, reduce the frictional resistance reduce the floating color, so as to effectively improve the fabric moisture friction color fastness.
Influence 1.5 softener
Increase reactive dye printing by soft finish color fastness. Softener having lubricating effect, can reduce the friction coefficient, thereby preventing the dye off. Cationic softener and anionic dyes may also be formed lakes, dyes not falling. Meanwhile, lake dye decreased solubility can improve wet rub fastness. But softener has a hydrophilic group is not conducive to improving the wet rub fastness. In the production practice, by using a dye fixing agent to seal the water-soluble group, control of finished cloth color fabric pH value to remove floating color, improve the smoothness of the fabric, thus improving moisture rubbing fastness. Pre-bake properly to avoid dye front "a spokesman shift." Note that factors alkali dosage, steaming time, the way water and adequate soap, etc., the first two and is closely related to the degree of hydrolysis of the dye, the latter two items and stained floating color is directly related to.
Dyed fabric, especially long car pad, to go through the full wash, soap and other processes to remove the fiber surface floating color and unreacted and hydrolysed dye, so as not to affect the color fastness, if not pay attention to post-dyeing treatment, It will result in poor color fastness, while darker shade will become wilt.
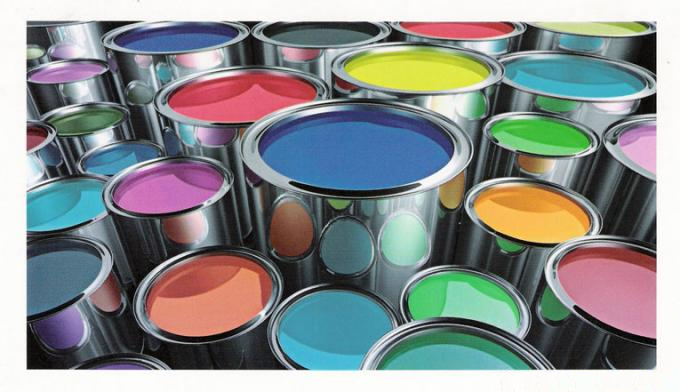
CHOOSE TIANYU,CHOOSE QUALITY